How to calculate the total manufacturing cost - formula, definition, and more
Learn how to calculate manufacturing cost using a simple formula. Understand all components of the formula and what they include.
by OneAdvanced PRPublished on 27 October 2021 13 minute read
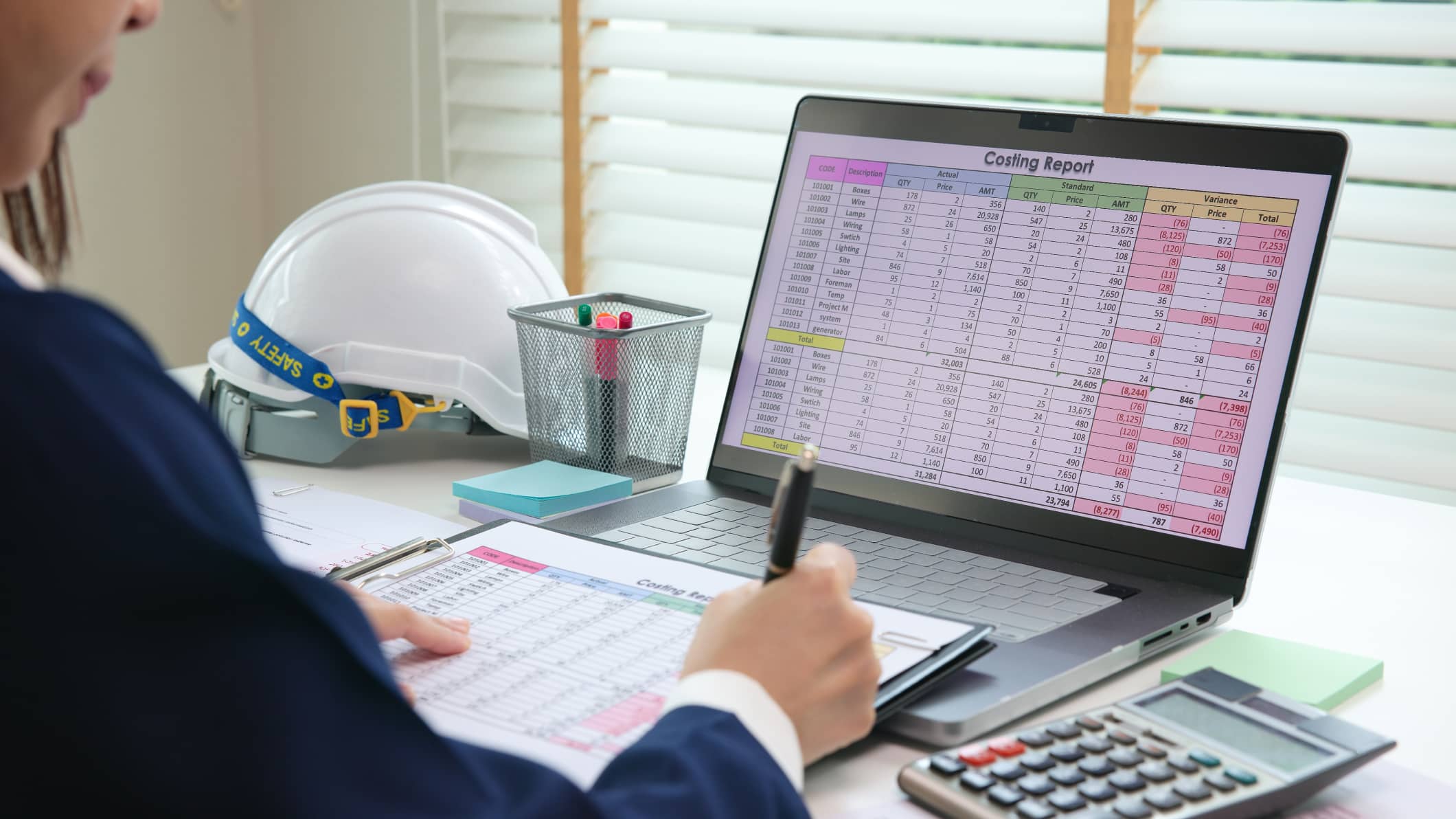
Simply put, total manufacturing cost is the overall sum of money required to manufacture a product. It is calculated by adding all the expenses incurred during production, which include the cost of direct materials, money spent on labour, and other overhead manufacturing expenses.
Having a direct impact on the cost of goods sold (COGS), gross margins, and the ultimate net profit, total manufacturing cost is a critical metric. When monitored closely, it can help identify inefficiencies and improve business outcomes. Considering its significance, let's dive into this article to understand what exactly it means, its components, how to calculate it and many benefits that come from knowing it.
What is total manufacturing cost?
Total manufacturing cost refers to the complete amount of money spent by a company on resources and its manufacturing operations in order to produce a finished good. Essentially, it represents the total cost of producing the goods that will be sold to customers.
Estimating manufacturing costs involves more than what may seem like just adding up expenses. It necessitates the accurate calculation of all cost components, which requires a thorough understanding of the entire production process, including every step and every expense, whether direct or indirect.
All expenses, no matter how small or seemingly unimportant, must be included as even small omissions could skew the total outgoing figures. To ensure this, it is crucial for the organisation to have visibility of the end-to-end process and all associated spending.
Total manufacturing cost formula
The formula to find the total manufacturing cost is as follows:
Total manufacturing cost = Direct materials + Direct labour + Manufacturing overhead
Here's how to calculate total manufacturing cost:
To use the formula effectively and determine the cost accurately, it’s essential to first determine the value of each of its three components correctly. To ensure this, we need to fully understand what each component entails. Let’s delve into each one and see how to calculate them.
Direct material
Direct materials are all the raw materials, components, or parts that are directly used in producing the finished goods. They typically become integral components of the product and can be easily traced back to it.
What is included in direct material?
It includes the cost of all the raw materials and inventory stock items that have been used in manufacturing the finished product. For instance, when manufacturing a simple T-shirt, fabric, thread, and labels are considered direct materials.
How to calculate direct material costs
For a T-shirt requiring 2 yards of fabric priced at £5 each, the fabric cost totals £10. If the thread used per piece costs about £1 and each label is approximately £0.50, then the total direct material cost will be £11.50.
In the context of manufacturing, the formula below is better suited for determining direct material costs:
Direct materials cost = (Beginning direct materials + Purchased direct materials) – Ending direct materials
Here,
Beginning direct materials refers to the cumulative value of raw materials already in stock.
Purchased direct materials is the price paid for new materials acquired during the production process, and
Ending direct materials is the value of raw materials remaining in stock at the end of the production process for a given timeframe.
Direct labour
It is the manpower and associated costs directly involved in the physical process of product creation, i.e., the labour needed to transform raw materials into a sellable good.
For example, the wages paid to employees directly involved in production. These employees include all workers on the assembly line (those who assemble items), machine operators, the processing team, supervisors, quality assurance inspectors, and even staff involved in warehousing and delivery.
What is included in direct labour?
Direct labour costs include not only wages but also any other expenses tied to their salary, including bonuses, taxes paid by the company, sick leave entitlements, worker's compensation insurance, and additional employee benefits.
How to calculate direct labour
To calculate the direct labour cost, first we need to determine:
- Hourly labour rate
It is the total of all wages (both regular and overtime), payroll taxes, and expenses related to employee benefits incurred by the company for those involved in production, divided by the total number of hours worked by them during the pay period. This rate can also be referred to as the labour cost per hour.
The formula to calculate the direct hourly labour rate is:
Hourly labour rate = (Total wages + Payroll taxes + Other benefits costs) / Total number of labour hours worked
When calculating, it is critical to factor in variables such as differences in pay among different workers and roles.
- Direct labour hours per unit
It is the number of working hours utilised by workers to manufacture a single product. It can be determined by dividing the total number of working hours (regular and overtime) by the number of units produced during a certain period.
The formula to calculate direct labour hour per unit is:
Direct labour hours per unit = Number of working hours / Number of units produced
With these two values, we can calculate the direct labour cost per unit using formula:
Direct labour cost per unit = Hourly labour rate x Direct labour hours per unit
To illustrate, consider the following data for the month of July for a T-shirt manufacturer:
- Total wages (including both regular and overtime): £1,500
- Payroll taxes: £200
- Other benefits costs: £100
- Total number of labour hours worked: 200 hours
- Total number of T-Shirts produced: 100 units
So, the hourly labour rate will be:
Hourly labour rate = (Total wages + Payroll taxes + Other benefits costs) / Total number of labour hours worked
Hourly labour rate = (1,500 + 200 + 100) / 200
Hourly labour rate = 1,800 / 200
Hourly labour rate = £9 per hour
And the labour hours per unit will be:
Direct labour hours per unit = Number of working hours / Number of units produced
Direct labour hours per unit = 200 / 100
Direct labour hours per unit = 2 hours per unit
With this, let's calculate the direct labour cost per unit:
Direct labour cost per unit = Hourly labour rate × Direct labour hours per unit
Direct labour cost per unit = £9 per hour × 2 hours per unit
Direct labour cost per unit = £18 per T-shirt
Manufacturing overhead
Considered an indirect cost, manufacturing overheads are expenses that are not directly related to the production of goods, but they are very much necessary for the production process to occur. Without these overheads, producing goods would not be possible.
What is included in manufacturing overheads?
It includes any operational costs that the business incurs to enable production. Expenses such as energy bills and rent are necessary because production cannot occur without power or a physical workspace. Additionally, costs associated with machinery breakages or depreciation are included in overheads. Other components include mortgage fees (if applicable), repair and maintenance expenses, production-related salaries, and depreciation of plant and equipment.
How to calculate manufacturing overheads
To calculate the total amount of manufacturing overhead, you need to first correctly identify and add all applicable overhead expenses. This total is often used to calculate the manufacturing overhead rate, which indicates the percentage of the company's revenue that goes toward covering manufacturing overhead costs.
For a given month, the manufacturing overhead rate can be determined by dividing the total manufacturing overhead costs for that month by the total monthly sales, then multiplying by 100.
The formula for calculating the manufacturing overhead rate is:
Manufacturing overhead rate = (Monthly manufacturing overhead costs / Monthly sales) x 100
For example, a T-shirt manufacturer might have the following overheads (with fictional monthly values for illustration)
- Factory rent: £500
- Utilities (electricity, water, gas, etc.): £150
- Depreciation of sewing machines and equipment: £100
- Maintenance and repairs: £50
- Indirect materials (Oil for machines): £30
- Insurance: £40
- Salaries for support staff like cleaners: £300
- Packaging supplies: £70 per month
- Miscellaneous expenses (Office supplies, administrative costs, etc.): £60
Total manufacturing overheads = 500 + 150 + 100 + 50 + 30 + 40 + 300 + 70 + 60
Total manufacturing overheads = £1,300
To calculate the total manufacturing cost per unit, we need to determine the manufacturing overhead cost per unit.
Manufacturing overhead cost per unit = Total manufacturing overheads / Total number of units produced
Manufacturing overhead cost per unit = £1,300 / 100
Manufacturing overhead cost per unit = £13
To summarise, here's what’s included in the total manufacturing cost:
- Direct materials: All the raw materials and resources used in the production process.
- Direct labour: The total manpower employed in the creation of the product.
- Manufacturing overheads: All the indirect expenses necessary for producing finished goods.
Now that we understand all the components of the formula, let’s calculate the total manufacturing cost per unit for the T-shirt:
- Direct material cost per T-shirt: £11.50
- Direct labour cost per T-shirt: £18
- Manufacturing overhead cost per T-shirt: £13
Using the formula:
Total manufacturing cost = Direct materials + Direct labour + Manufacturing overhead
Total manufacturing cost = £11.50 + £18 + £13
Total manufacturing cost = £ 42.50 per unit
What are the benefits of calculating total manufacturing cost?
Lower costs
It may seem obvious, but by being aware of all the expenses involved in your manufacturing operation, it becomes more possible to reduce these costs. Total manufacturing costs could highlight expenses that are completely unnecessary (and can therefore be eradicated completely).
It may also shine a light on costs that have, over time, become extortionate without you realising. This newfound visibility around spend could lead to a renegotiation with suppliers, to attain cheaper deals. Or you may research some other potential partners, who can provide you with a better price (whilst supplying you with equally good materials).
You may also decide to reduce overheads if they’re higher than expected. This could involve searching for a cheaper energy provider or finding a more cost-effective location (where the rent is not quite as high). It essentially enables you to improve your spending methods.
More clarity around financial health
Manufacturers that don’t possess an accurate picture of spend will often have a distorted perception of their financial health, which could cause them to budget poorly. Total manufacturing cost, when compared with income and revenue, provides clarity around profitability and overall business performance.
If your findings in this area aren’t favourable, you can at least use the data as fuel to remedy the situation. This information will dictate key decisions around your company’s direction, such as whether to be cautious or bold (and therefore whether to make cuts or to invest in core functions).
Informed decisions around pricing
The profitability picture gained from total manufacturing cost will also govern other strategies too, such as your approach to sales and pricing. If your profits are not at the desired level, you may determine that the current sales model isn’t working and that you perhaps need new methods or to open new sales streams (such as e-commerce).
If you conclude that costs are as low as possible, but revenue is still struggling, the next step could be to alter your pricing. If you set prices too high, customers may go to competitors where they can find a better deal. Equally, if prices are too low, you won’t be generating the required revenue to make your business profitable.
A fine balance must be struck, in terms of setting a price that falls within the market norm, but also retrieves an acceptable return (based on the investment that went into producing each good).
Less waste
When looking at total manufacturing cost, you might not only learn that the materials being bought are too expensive, but also that excessive quantities are being bought unnecessarily. By analysing the amount of excess that is usually generated during production, you can use this to adopt a more sparing approach to purchasing.
This not only has financial benefits but improves your environmental standing too (as you will produce less waste if you only have the materials you need). By having less produce in the warehouse at any given time, fewer storage costs are incurred, and your facility is far more organised as a result. There are some well-known stock control strategies (such as lean manufacturing) that can be utilised to achieve these outcomes.
Insights that drive efficiency
Actions that reduce costs can often streamline your processes as well. Removing steps from the production process to save money also increases efficiency, ensuring that items are created faster (which leads to greater customer satisfaction).
Another example is sourcing materials from local suppliers. This may lower expenses due to cheaper delivery, but it also ensures a quicker turnaround for your supply chain, making it possible to meet expectations even when last-minute orders are placed.
By searching for more cost-effective machinery/technology, you could stumble upon mechanisms that are far more sophisticated than your previous methods, and therefore provide a much greater ROI (return on investment).
How can OneAdvanced help with total manufacturing cost?
To work out total manufacturing cost accurately (and to gain the associated benefits), you must have a simple and effective system for capturing all cost-related data. It’s a completely counterproductive endeavour if the information gathered is inaccurate, inconsistent, or outdated in any way. But this is where software can help.
Cloud solutions enable you to work from anywhere, at any time, meaning you shouldn’t miss a trick when it comes to spend. But remote access aside, Manufacturing software’s real strength comes from the fact that it unites all your business functions, allowing every employee to complete work within the same system.
This cohesion leads to powerful data, that can be reported on, analysed, and used for important strategic decisions. It’s much easier to work out total manufacturing cost when the latest financial data can be accessed at the click of a button, and when the information from all departments is inter-connected.
If you’re looking for a simple and accurate way to monitor total manufacturing cost, whilst also bringing all your business functions together in one place, then take a closer look at our Manufacturing software solutions.
FAQ
What is the difference between direct and indirect manufacturing costs?
Direct costs are typically variable expenses that change depending on the period and amount of production taking place, while indirect costs are usually more constant, as they are often fixed in advance (such as overheads like rent).
So, what exactly constitutes an indirect cost? In terms of indirect materials, these are resources that don’t necessarily form part of the finished product. They might not be directly traceable to the finished product and wouldn’t typically appear on a bill of materials. Examples could include glue, water, cleaning products, or any other materials used at some point during production.
Regarding indirect labour costs, these are wages paid to employees who weren’t physically involved in manufacturing but still played some part in the process. This could include a supervisor, manager, or cleaner, for example, who would be involved in the planning, orchestrating, and maintenance of production.
What is the difference between total manufacturing cost, COGM and COGS?
Total manufacturing cost shouldn’t be confused with cost of goods manufactured (COGM) or cost of goods sold (COGS), which are slightly different terminologies. COGM is a formula that only considers the costs associated with items that finished the production process and became sellable products.
COGS calculates the costs of items that not only finished the product creation journey but also got sold to a customer. In contrast, total manufacturing cost includes any production costs within a window of time, regardless of what was finished or sold.
What is total manufacturing cost per unit?
Total manufacturing cost per unit is the amount of money required to produce a single unit of a product. It includes all the direct costs (materials and labour) and indirect costs (overheads) incurred by the company to manufacture one finished product. You can determine the cost of producing one unit by dividing the total manufacturing cost by the total number of units produced during a specific period.
Formula for total manufacturing cost per unit is:
Total manufacturing cost per unit = Total manufacturing cost / Total number of units produced
Where:
Total manufacturing cost = Direct materials cost + Direct labour cost + Manufacturing overheads
Total units produced is the total number of finished goods manufactured during a specific period.
How to find total manufacturing cost incurred during the year?
To find the total manufacturing cost incurred during the year, you need to simply add up all the direct and indirect costs associated with manufacturing the products throughout the year. This includes all the direct material costs, labour expenses, and manufacturing overheads spent that year.
What are the three components of total manufacturing cost?
The three main components that make up the total manufacturing cost are direct materials cost, direct labour cost, and manufacturing overheads (comprising all the indirect expenses associated with manufacturing).
Is total manufacturing cost the same as manufacturing overhead?
No, they are not the same. Total manufacturing cost includes every expense involved in producing a product, whereas manufacturing overhead, representing only the indirect costs, excludes direct materials and labour, making it just a component of the broader manufacturing cost.
About the author
OneAdvanced PR
Press Team
Our dedicated press team is committed to delivering thought leadership, insightful market analysis, and timely updates to keep you informed. We uncover trends, share expert perspectives, and provide in-depth commentary on the latest developments for the sectors that we serve. Whether it’s breaking news, comprehensive reports, or forward-thinking strategies, our goal is to provide valuable insights that inform, inspire, and help you stay ahead in a rapidly evolving landscape.