The importance of production planning in manufacturing
What is production planning and why is it so important? In this piece, we answer these questions, and highlight the key steps involved in creating a production plan.
by OneAdvanced PRPublished on 7 September 2021 7 minute read
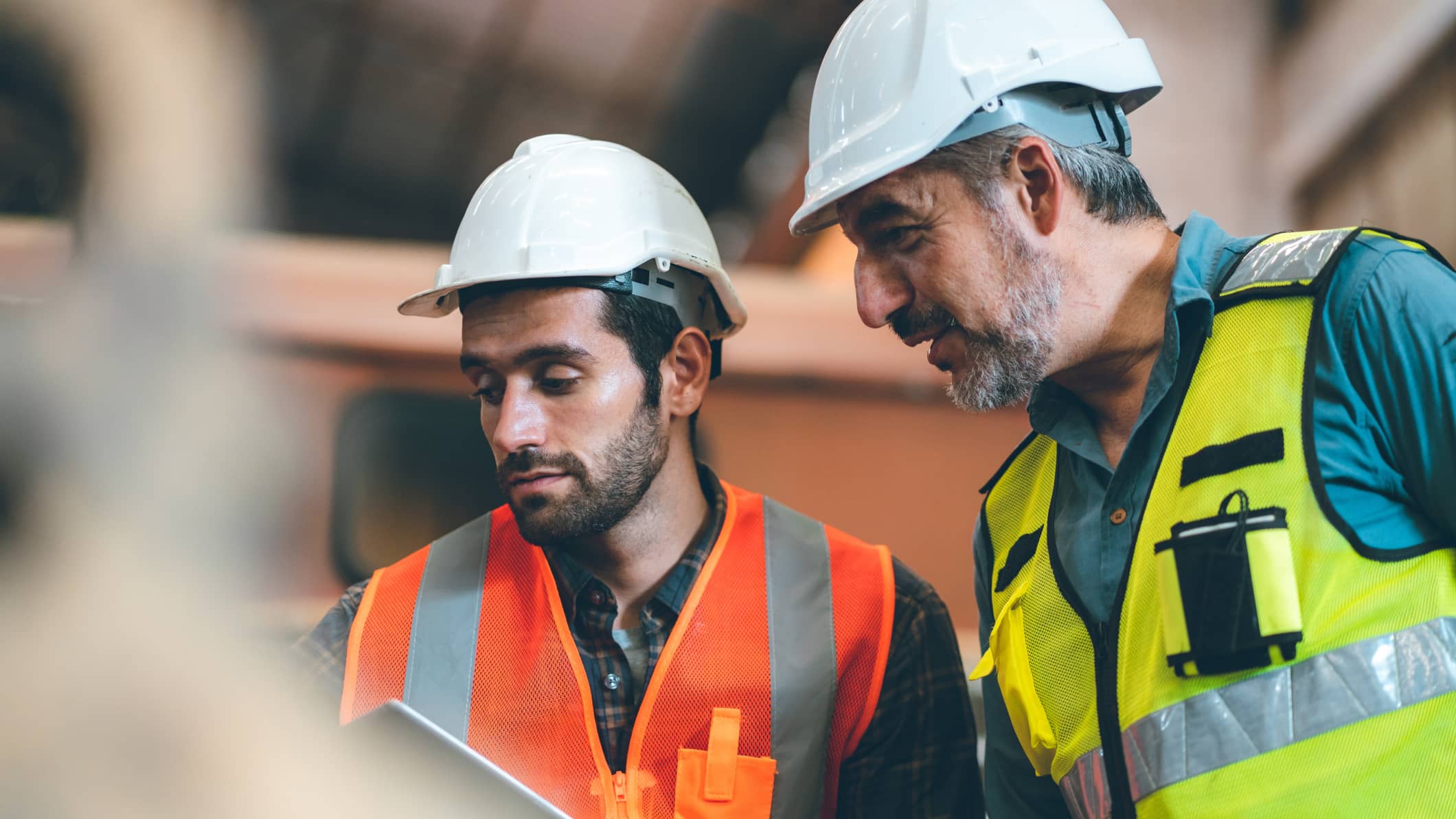
Production is one of the most important processes within manufacturing, and is a core part of what it means to be a manufacturer. Without this activity, no finished goods would be created, and there would be nothing to sell to customers.
It’s therefore crucial to have the right methods in place to complete it well, which is where production planning comes in. But what exactly is it, and why is it important?
In this article, we highlight the different steps of production planning, discuss how it differs from production control, and explain how software transforms the way it can be done.
What is production planning?
Production planning has the purpose of ensuring all necessary preparation is completed before a production cycle begins, so it can run smoothly. This involves allocating resources effectively so that everything is in place for each stage of production to start.
The factory floor should be organised appropriately. All machinery should be in its rightful position, employees should know when they are required, and the right materials should be on hand for when they’re needed.
It sounds obvious, but planning is beneficial in most walks of life. It gives you a picture of what is to come, so that there are less unexpected results. And it allows for a higher degree of control over any situation too.
At least one person within a manufacturing business should oversee production planning (perhaps a factory floor manager). Accountability like this makes it more likely the obligation will be completed.
Some of the benefits that come with production planning include:
- Decreased errors
- Fewer bottlenecks
- Deliver more on time
- Less downtime
- More organised workspace
- Fewer defects
- More efficient use of stock
What is the role of production planning in manufacturing?
Production planning essentially enables manufacturers to map out the entire chain of events, starting with a raw material, all the way through to its transformation into an end-product. By having a clear picture of how events will unfold, it’s easier to avoid bottlenecks that would otherwise halt production. You’re also less likely to be wasteful, and more likely to stick to an expected amount of spend.
By visualising the journey of goods, defects become less commonplace, and the output tends to be of a higher quality. Production planning is linked to risk management in some ways, as you may stumble across hidden problems (such as a faulty machine or a gap in the production chain).
Planning will give you an idea of how long each production cycle will take, which in turn makes it easier to stick to deadlines. It also allows you to see what materials are needed to produce each item. When coupling these aspects with customer demand, it should be simpler to figure out exactly what needs to happen (and when).
At the earliest opportunity you should select an appropriate production method, of which some examples include:
- Batch production
- Flow production
- Continuous production
- Job production
Production planning vs production control
Production planning, production control, and production scheduling can often be mistaken for one another. But it’s important to distinguish these terms. As we’ll come on to in the next section, production scheduling is one component of the entire planning process. It is largely concerned with the timings of production.
Production control on the other hand comes about as a result of successful planning and scheduling. It’s specifically when you have full control over the manufacturing process, by having a clear view of all the moving parts.
In this scenario you’ll likely have smart systems in place, with effective ways to monitor inventory, equipment, employee schedules and the factory floor layout. Even if something unexpected were to happen, you’d hopefully have the data to identify the cause, so that the situation could be rectified quickly.
What are the main steps of production planning?
Preparing
The first step is laying the initial groundwork, which provides a foundation for everything that follows. This includes notifying the appropriate people about upcoming production runs. They should be given details of the order size, as well as the due date. Another part of preparation is sourcing the right materials (and the right quantities) from suppliers to complete the customer order in full. Machinery should be checked before any production run to ensure it is in working order.
Routing
Following this you should create a logical route for your production run. This involves knowing each piece of machinery that a material needs to interact with on its way to becoming a sellable good (and the order in which it must complete this journey). The location of any machinery should be influenced by this path, so that things can flow as smoothly as possible. Over time you may make alterations if you find more optimal routes.
Scheduling
The next part of the plan is to determine the schedule, which, as we’ve already touched on, is deciding exactly when each part of production will take place. Once the route is determined, it’s far easier to decide when each activity should occur. A schedule is crucial for any plan, as it turns it from an abstract idea into a concrete action. It also means that employees will know when they’re obligated to complete their role in the process. And the relevant equipment can be booked in advance to fall in line with this schedule.
Dispatching
Following this you must dispatch production details to the right people. This can include work orders for the production run. On top of the route and schedule you may need to also provide further instructions so that products can be created seamlessly. Perhaps there are designs that need to be seen before an item can be assembled. Workers may need some form of documentation to show when they’ll have access to certain tools. A final dispatch may involve the person in charge giving the go-ahead so production can begin.
Reviewing
The final step involves looking at the previous stages to see if anything has been missed (or could be done better). This part of the plan is crucial, as it serves as a safety net, and a chance to enhance operations even further. The beauty of planning is that you may uncover some inefficiencies along the way, which may have otherwise remained hidden (and could have potentially harmed productivity if left unfound).
What are some tools I can use for production planning?
Some production planning tools will be more suitable than others, depending on the scale of your operations. Smaller manufacturers may be happy to carry out this activity via more traditional means (such as pen and paper). But, for any business, this can be a risky approach. If these documents were to be damaged or misplaced, the whole plan would be lost. Not only this, but production planning is complex too, so to do it by hand would take a lot of time and effort.
Some companies may use a spreadsheet instead, which is certainly a step up. But this approach comes with its own flaws. Spreadsheets aren’t specifically designed for production planning. They have wide-ranging functionality and typically begin as a blank canvas. This means you must have a lot of expertise to achieve the specific outcomes you desire.
Using dedicated MRP software is likely to give manufacturers the best result, as it will have specialised functionality and designated fields to record production planning data. Some SMEs will feel that cost rules them out of this option. However, their investment would likely be paid due to the transformational results such systems bring about. The next question, of course, is which MRP solution is best for manufacturers?
When it comes to production planning, you’ll want a system that allows you to schedule work orders. It should also provide you with instant updates on any active production runs, as well estimated timeframes for completion. You should have full visibility of where different orders are currently sitting in the creation process. This can then be passed on to customers which will improve customer service.
With production being connected to your finances, online sales, inventory levels, customer details and more, you suddenly have a much more cohesive set-up (with more accurate and consistent data). Not only this, but you can then automate certain tasks too, and enjoy enhanced performance as a result.
When you combine this high-quality data with the software’s powerful reporting capabilities, you can analyse your production methods in far more detail, implementing changes that increase efficiency, and making bold forecasts that could help you to achieve growth.
If you're looking to enhance your production planning process, then take a closer look at our Manufacturing software solutions.
About the author
OneAdvanced PR
Press Team
Our dedicated press team is committed to delivering thought leadership, insightful market analysis, and timely updates to keep you informed. We uncover trends, share expert perspectives, and provide in-depth commentary on the latest developments for the sectors that we serve. Whether it’s breaking news, comprehensive reports, or forward-thinking strategies, our goal is to provide valuable insights that inform, inspire, and help you stay ahead in a rapidly evolving landscape.